Modern pump manufacturing uses robotics and automated inspection systems to improve efficiency and consistency.
- Amerigo Exports
- Dec 16, 2024
- 2 min read
The manufacturing of centrifugal pumps involves several stages, combining engineering design, material selection, precision machining, assembly, and quality control. Here's an overview of the typical process:
1. Design and Engineering
Requirement Analysis: Engineers determine the pump specifications, such as flow rate, head, pressure, and fluid compatibility.
3D Modeling: Computer-aided design (CAD) software is used to create detailed 3D models of the pump, including the casing, impeller, and shaft.
Simulation: Computational fluid dynamics (CFD) simulations are performed to optimize performance, minimize turbulence, and improve efficiency.
2. Material Selection
Pump Components: Materials are chosen based on the application. Common choices include:
Casing: Cast iron, stainless steel, or bronze for corrosion resistance.
Impeller: Stainless steel, bronze, or specialized alloys for wear resistance.
Shaft: High-strength steel or stainless steel.
Seals and Bearings: Materials like carbon, ceramic, or elastomers.
Specialized Needs: For aggressive chemicals, exotic alloys or polymers may be used.
3. Pattern and Casting (for Casing and Impeller)
Pattern Creation: Patterns of the casing and impeller are made using wood, metal, or plastic.
Mold Preparation: Sand or investment molds are prepared based on the pattern.
Casting: Molten metal is poured into the molds to form the pump casing, impeller, and other parts. After cooling, the casting is removed, cleaned, and inspected.
4. Machining
Precision Cutting: CNC (Computer Numerical Control) machines are used to achieve exact dimensions and smooth surfaces.
Key Machining Steps:
Impeller trimming for precise dimensions.
Boring and threading of the casing for inlet/outlet connections.
Machining of the shaft for perfect alignment.
Balancing: Rotating parts, especially impellers, are dynamically balanced to minimize vibrations.
5. Assembly
Component Installation: The machined parts, including the impeller, shaft, bearings, and seals, are assembled.
Shaft Alignment: Proper alignment of the shaft ensures smooth operation.
Seal Installation: Mechanical seals or packing are installed to prevent leaks.
Casing Closure: The casing is bolted or sealed shut, with proper torque applied.
6. Testing and Quality Control
Hydraulic Testing: The pump is tested for flow rate, head, and efficiency under various operating conditions.
Pressure Testing: Ensures the pump casing can withstand design pressure without leaks.
Performance Validation: The pump is run at full speed to check for noise, vibration, and bearing performance.
Non-Destructive Testing (NDT): Methods like X-ray, ultrasonic, or dye-penetrant testing are used to identify flaws in the materials or casting.
7. Coating and Finishing
Surface Treatment: The pump may be coated for corrosion resistance (e.g., epoxy or powder coating).
Polishing: Impellers and other internal components are polished to reduce friction.
Painting: Exterior surfaces are painted as per the customer's requirement or to prevent environmental damage.
8. Packaging and Delivery
Pumps are cleaned, lubricated, and packaged to prevent damage during transportation. Documentation, including manuals, test certificates, and warranties, is included.
Advanced Manufacturing Considerations
Additive Manufacturing: Some manufacturers use 3D printing for rapid prototyping or producing small components.
Automation: Modern pump manufacturing uses robotics and automated inspection systems to improve efficiency and consistency.
This process ensures that the final centrifugal pump meets the necessary performance, durability, and safety standards.
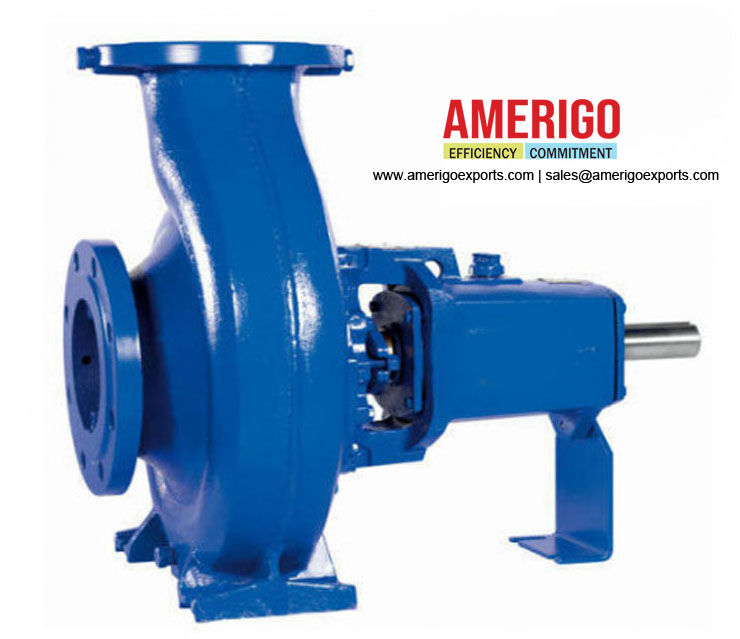
Comments